In many areas of production, in environmental protection or even in home, metal needs to be protected against corrosion. A sample way of doing this is to apply an anticorrosion point. In a large number of applications, through, the protection this provides is insufficient; higher- quality industrial materials are required.
There are basically two routes available:
- The equipment items requiring protection can be fabricated entirely from a resistant material.
- The mechanical strength of the equipment items is attained with a low cost material (steel) and the corrosion resistance is achieved with a lining made of suitable material, e.g. rubber.
Rubber lining are highly efficient. In combination with an appropriate base material usually steel they provide very reliable surface protection. They are a safe, trouble free and reliable means of combating corrosion and in special cases, abrasion.
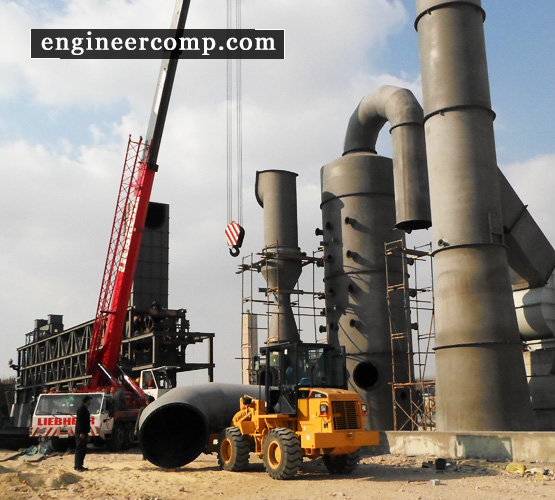
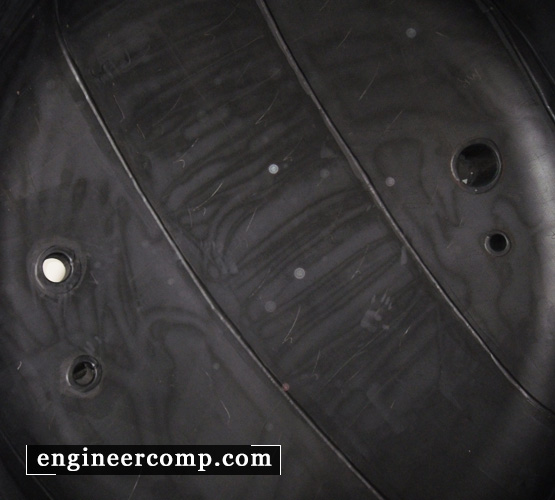
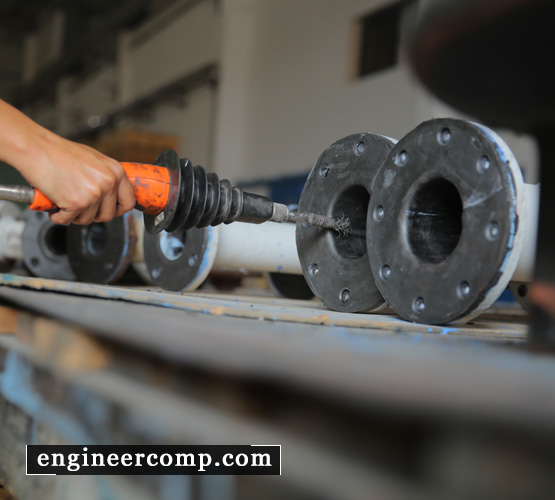
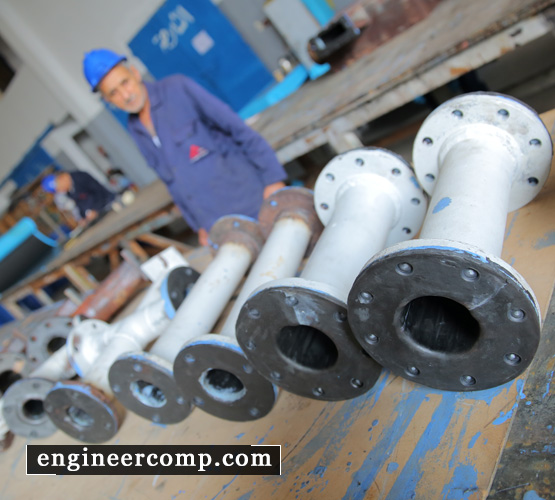
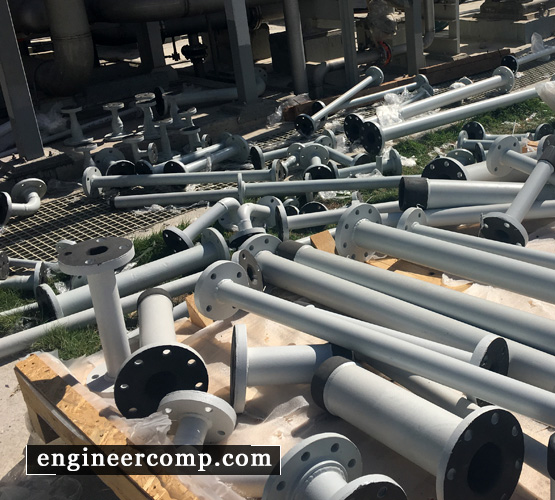
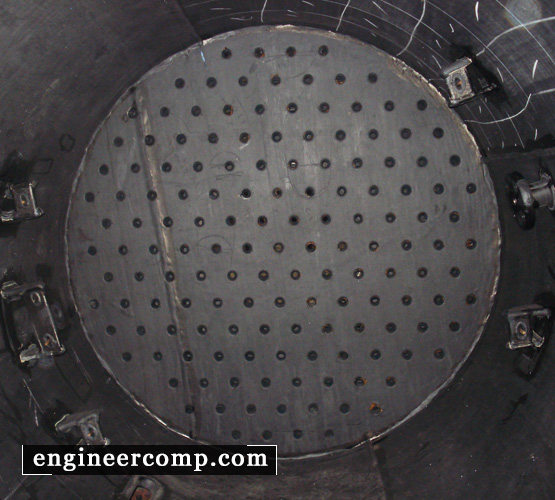
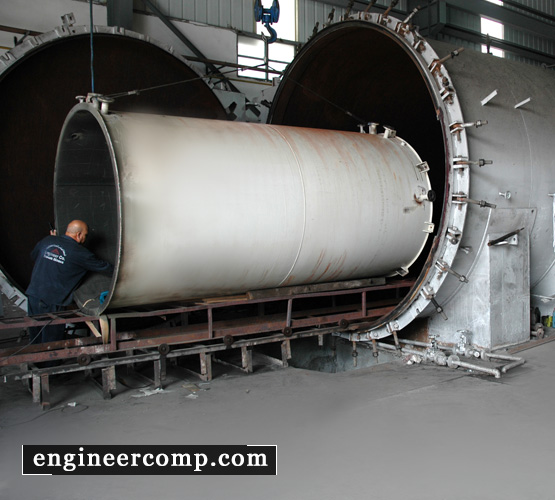
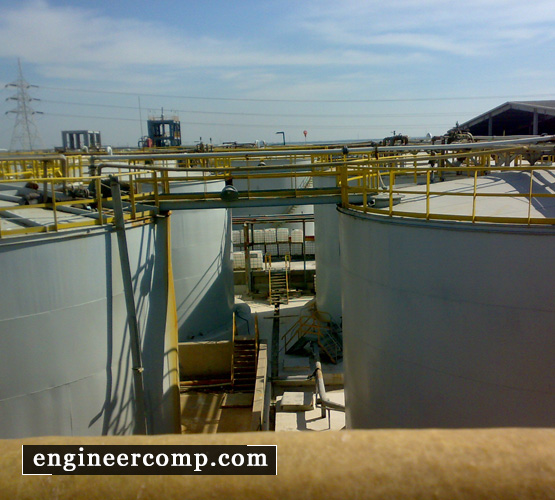
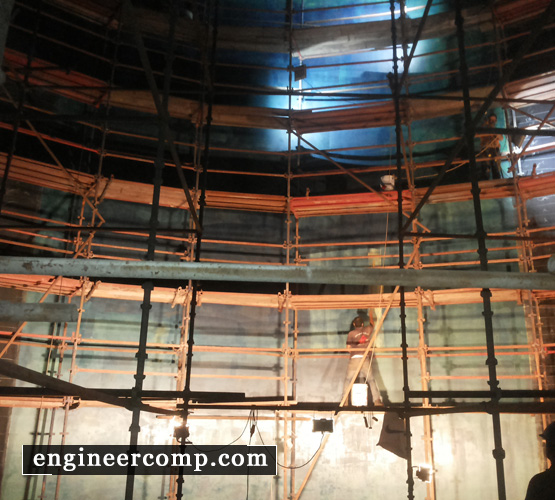
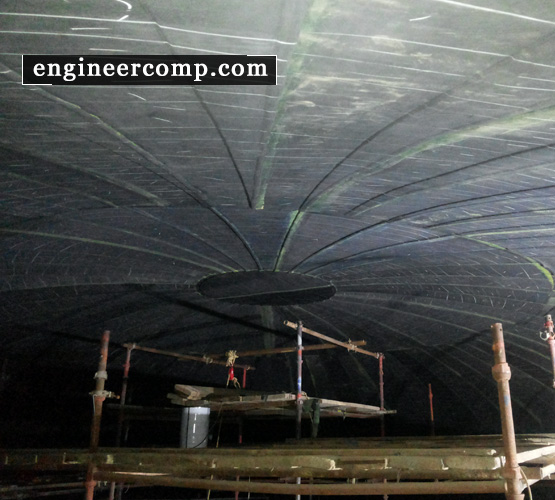
The use
of Rubber Lining
Rubber lining used in various areas:
- Medium and large size process equipment fabricated from steel, such as storage tanks, absorbers, bulk transportation containers, evaporators, pipe work, etc.
- Process equipment exposed to the action of aggressive corrosive liquids and gases – e.g. salt solutions, HCL, phosphoric acid.
- Process equipment for waste water treatment plants.
- Pressure and vacuum vessels.
- Chlorine electrolysis cell.
- Agitators.
- Filters.
- Valves.
Rubber lining types..
In the field of rubber linings, two different forms of the material are essentially used:
- Firstly, hard rubber / ebonite linings, i.e. highly cross-linked elastomers based on isoprene or styrene-butadiene rubbers. These linings are characterized by excellent diffusion resistance to highly diffusive corrosive media.
- Secondly, soft rubber linings i.e. cross linked elastomers (usually butyl rubbers) with good diffusion resistance and good to very good chemical resistance to aggressive and corrosive chemicals.
The suitability of the lining material is determined by:
- Its resistance attack.
- Its bond with the steel (vulcanization of the rubber and the bonding system only occurs if the rubber sheet is applied in the unvulcanized state. This technology provides a bonding strength far superior to that of conventional adhesive bonding systems).
- Hard rubber or soft rubber is used depending on the conditions of the project.
color | Grey silver | ||
Density | g/cm | 1.22 | ASTM D 297 par. 15 |
Hardness shore | D | 78 (+ or -) 5 | ASTM D 2240 |
Tensile strength | MPa | (> or =) 20 | ASTM D 2707 |
Elongation | ٪ | (> or +) 3 | ASTM D 2707 |
Martens grade | C | 53 | UNI 4281 |
Compression resistance | MPa | 67 | UNI 4279/72 |
IZOD impact test - With cut - Without cut | N N/mm | 17.4 6.5 | ASTM D 256 met. A ASTM D 256 met. A |
Max unit load | MPa | 82 | ASTM D 790 |
Adhesion to metal | MPa | (> or =) 12 | ASTM D 429/A |
Max service temperature | C | 100 |
properties | unit | value | standard |
Steam vulcanization | 4h @ 140 C by steam pressure | ||
color | Black | ||
density | g/cm3 | 1.26 | ASTM D 297 par. 15 |
Hardness | A | 53 (+ or -) 5 | ASTM D 2240 |
Tensile strength | MPa | (> or =) 9 | ASTM D 412 |
Elongation at break | % | (> or = ) 640 | ASTM D 412 |
Tear strength | N/mm | (> or =) 48 | ASTM D 624 |
Modules at 200% | MPa | (> or =) 2.5 | ASTM D 412 |
Abrasion resistance | mm3 | (< or =) 160 | DIN 53516 |
Adhesion to substrate | N/mm | (> or =) 5 | ASTM D 429/E |
Max. operating temperature | C | 110 |
Why choose our services ?
We are always at your service
We have special repair systems available for all materials:
- Repair pastes for small areas.
- Rubber sheeting for medium sized area.
- Facilities for carrying out large area repairs on site.
Uses test methods which conform to international standards
During application:
- Fitness of surfaces for rubber lining.
- Climatic conditions.
- Visual appearance.
- Imperiousness.
At final inspection:
- Shore hardness.
- Thickness of rubber lining.
- Acoustic testing to detect lack of bonding.
- Visual examination for irregularities.
- Imperviousness by the high voltage test method.
- Spark test by holiday detector.